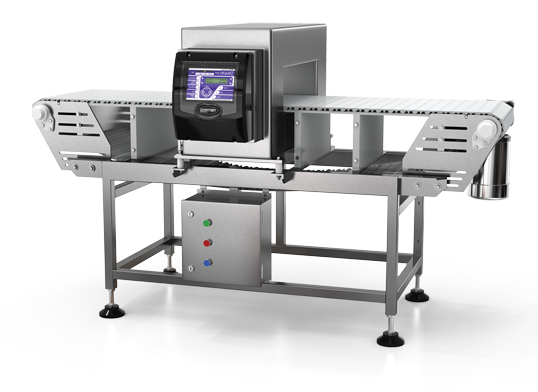
Metal Detector Setup
March 28, 2019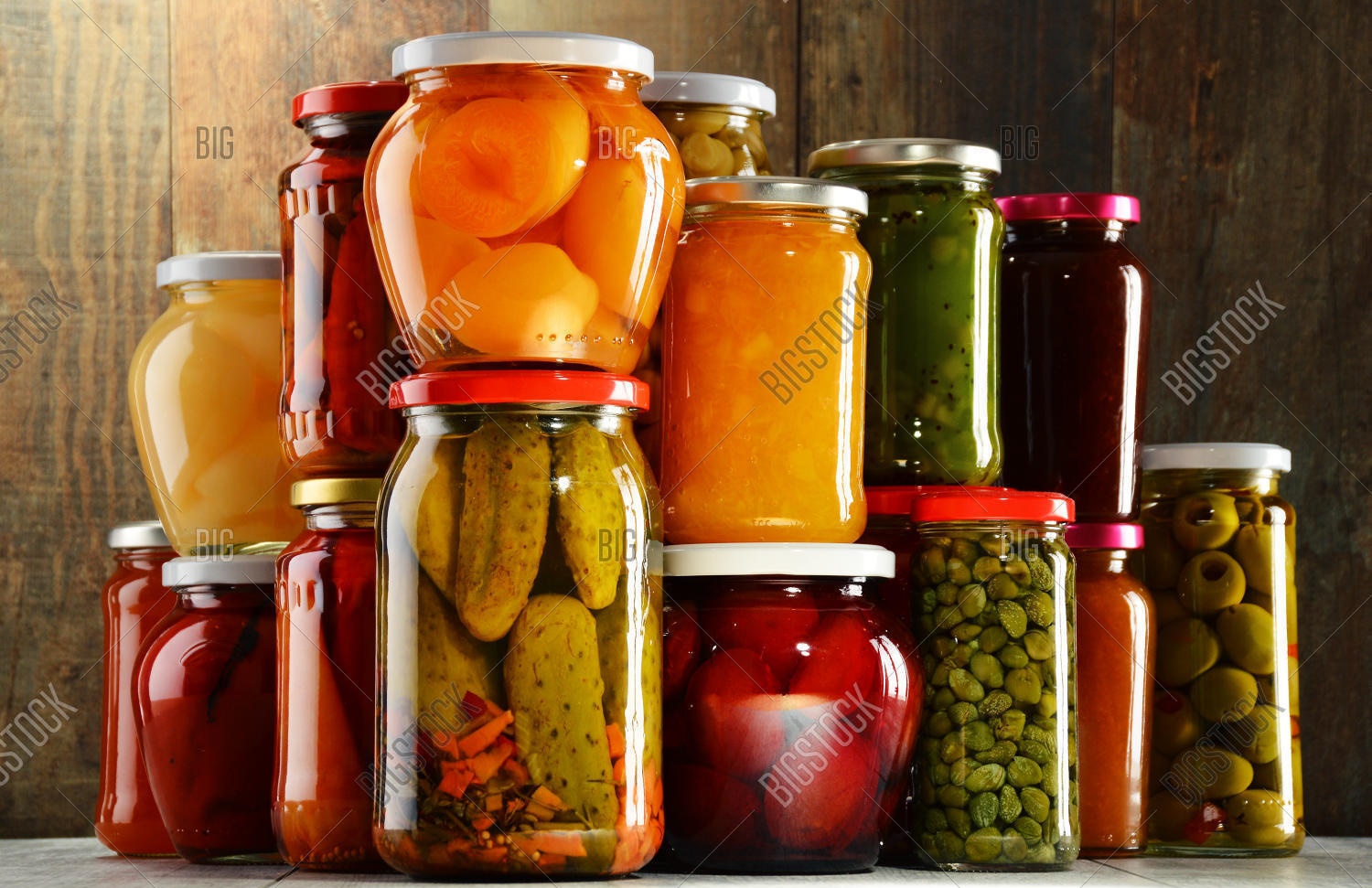
What’s New With The Food Safety Guidelines
June 3, 2019Why Regal Considers Customer Service Critical
In a culture that often equates money with success, the importance of customer service seems like a long-lost art. But at Regal Packaging Services, we believe that customer service is critical to our success. Customers, especially in the food industry, need to know that we stand beside and behind them. What they do in producing or packaging their product and in food safety is important to us. And it’s important to the consumer at the local grocery store.
To that end, our processes and procedures are designed to do just that. We have the knowledge and expertise that our customers need to succeed. Here’s an example:
What We Need to Know
A customer called and inquired, “What size test standards should I be using?” Before we can answer the customer, we have to ask a few questions in return:
- What is your product?
- Is the product frozen or chilled?
- Is the product wet or dry?
- How is the product run through your metal detector?
- Is the product boxed, bagged or uncontained?
- What kind of metal detector do you have?
- What size is the aperture of your metal detector?
- Where are you placing the test standard?
Experience and Certification
Our salesman and service technicians have decades of experience. So once those questions are answered (among others), we can provide a starting point. In other words, we can tell the customer, “You should be able to achieve…” If a company’s customer service representative doesn’t have access to that knowledge base, the customer is left in a quandary. And no other company that makes test pieces can provide that. Collectively, Regal has nearly a century of experience in metal detection and x-ray inspection.
Our Testrods Division is ISO 9001:2015 Certified,. That means we have a Quality Management System (QMS) in place to maintain a set of production, inspection and quality control procedures. Our policies ensure our customer gets a product they can trust. We are continually striving to provide metal detection and x-ray inspection verification test pieces we know will work on the production line.
If our processes gets haphazard, it could mean that a consumer gets contaminated food at the family dinner table.
Process
Our procedures ensure that:
- Each lot of metal balls received from our supplier is NIST certified by size. And that they are thoroughly tested for accuracy, consistency and detectability.
- Every acetal molded test pieces is verified for no trace of metal that might affect the final standard of measurement. Acetal molded pieces are certified as food grade safe nearly indestructible, with a melting temperature over 300°F.
- Molded test pieces are engraved with size and type metal, including certificate number and our company information. You’ll always know where your test pieces come from and where to find answers to your questions.
- The metal sample will remain intact, safely encased without concern that it will end up somewhere in your product.
- The adhesive used in the manufacturing process to encapsulate the metal standard has an application temperature over 350°F. Its softening point will be 194°F and it is FDA approved for food contact.
- Before test pieces are sent to you, each piece is verified as having the correctly engraved information. Your test pieces can be incorporated in your quality control process without worry. Test pieces are also checked to before shipping to meet our rigorous standard of excellence. This includes a final test in a live metal detector to ensure proper levels of detectability.
- All products are guaranteed against manufacturing defects, and even custom products are returnable. Should a return be necessary, we promise to act quickly and efficiently in getting the correct product in your hands.
The Final QA Check
At Testrods.com, we check, double check, triple check then re-check to mitigate against any kind of safety issue. We value our customers’ business, and, more importantly, the safety of their customers! Since we back our products with honesty, integrity and dependability, we believe we are the most trustworthy source of test pieces on the market. And ISO Certification is part of the evidence to support that claim.