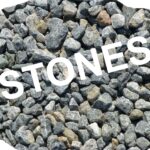
Stones
June 1, 2024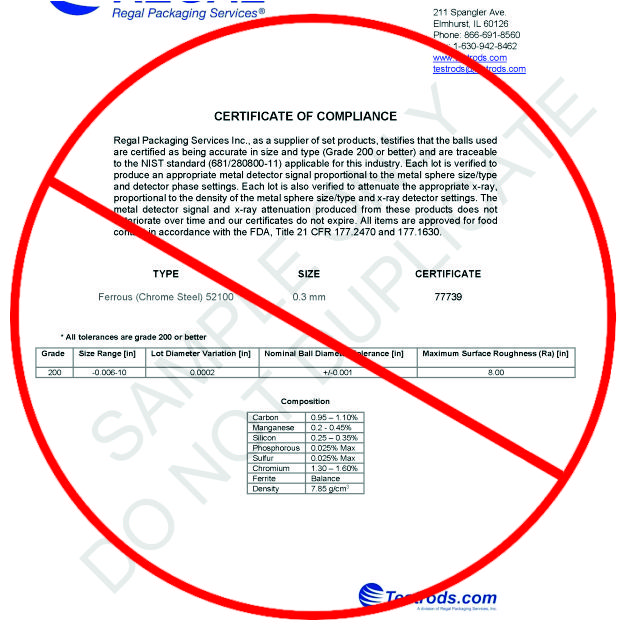
Is There an Expiration Date for Certificates of Compliance?
August 1, 2024
The People Behind the Metrics of Quality Control
My first foray into the metrics of quality control and food safety was during a time when I was unemployed for three years. A friend recommended me to a company that did x-ray inspection for other food plants. The product being inspected was on hold because the customer either had a problem with their inspection systems or it needed to be retested for suspected contaminant.
This company employed people who were either out of work or at some other stage of life where they needed or wanted additional income. However, the employee selection always reflected a strong work ethic and a willingness to maintain high standards of quality control.
The packaged food was placed on a conveyor, passed through a medical grade x-ray machine, was viewed on a screen (in a booth) by the quality control worker, rejected as needed and then replaced in its larger box and onto a pallet. It was the job of the viewer to assess the image on the screen and determine whether there was a contaminant.
The metrics of quality control were safeguarded carefully by collecting (rejecting) the product before and after the item with suspected contaminant. These items would later be rescanned to determine, in a second pass, if an impurity was still detected. It was the watchful eye of a trained technician that captured contaminated product in order to keep it out of the marketplace.
Another way to manage the metrics of quality control was to run the line a great deal slower than you would find on an industrialized line with an automatic x-ray system. Given that the product was on hold, this was a necessity, and even preferred. In addition, a “test” package was sent through the x-ray to make sure the operator was capable of rejecting what the expected contaminant looked like. For instance, if the suspected pollutant was a 1.0mm Stainless Steel 316 object, then that same size (or smaller) would be used for testing. If the operator missed the test, then all product since the last test would be reinspected, just as it should be in a food plant.
Three years later, I began working as the Sales and Quality Manager for Regal Packaging Services. I discovered that my time “in the booth” was extremely helpful in understanding what companies were expecting to accomplish when in quality control testing both in x-ray inspection and in metal detection. I already understood the metrics of quality control. I recognized how critical it is to manage a production line right down to the lowest or smallest part of the process.
Along with our sales and service team, we bring nearly 100 years of experience to the job, so we can offer expertise that other companies who are in the business of selling “metal detectable products” just can’t offer.
In addition, we have worked to maintain ISO 9001:2015 certification, demonstrating our commitment to excellence in product quality and cutting-edge innovation in the industry. We are consistent, dependable, and focused on our part in setting a high level of metrics for quality control in the food safety chain. Ten years into the job, I realize I couldn’t have imagined having an influence of any kind in the food industry.
As we have worked with our customers, we’ve gone from offering four types of certified contaminants to seventeen, including what we believe is the best bone simulate available on the market. As a result, over those same ten years, we have tripled our revenue. We know that is a direct result of hiring the right people and training them appropriately.
At every level, we want our employees to be ahead of the industry, responding to customers’ inquiries about how to successfully meet the needs of their application. At times, we put them in touch with our metal detectors salespeople, technicians and auditors who provide guidance based on decades of field experience. Those same people bring back their experience to the Testrods team to help us navigate the ins and outs of a wide variety of metal detection and x-ray inspection challenges. We’ve also been known to visit assorted plants to see what they are doing first-hand.
In fact, our first venture into bone simulate products came as the result of a visit to a nearby, nationally known meat processing and packing company. We were able to provide them with a multi-card containing an array of sizes and thicknesses of contaminant which they could view and compare with the typical bone they were expecting to find at the end of the production line.
Most companies selling metal detection and x-ray inspection verification test pieces are also selling a host of other products. They leave the details up to their providers and essentially serve as a middleman in the food safety picture. That’s not to disparage any of their products or services. They just don’t have the time or resources for their staff to be experts in the industry. At Testrods.com we’re passionate about providing the right tools for the food industry.
In the end analysis, keeping food safe is more than just machines, tools, processes, procedures, or systems. It is about the people who manage these things, people who care about the quality of their work and how it impacts their own families and friends. So, when you get right down to it, you have to ask yourself, “Am I the right kind of person to fit into the metrics of quality control?” Call us at 866-691-8560 or email testrods@testrods.com.