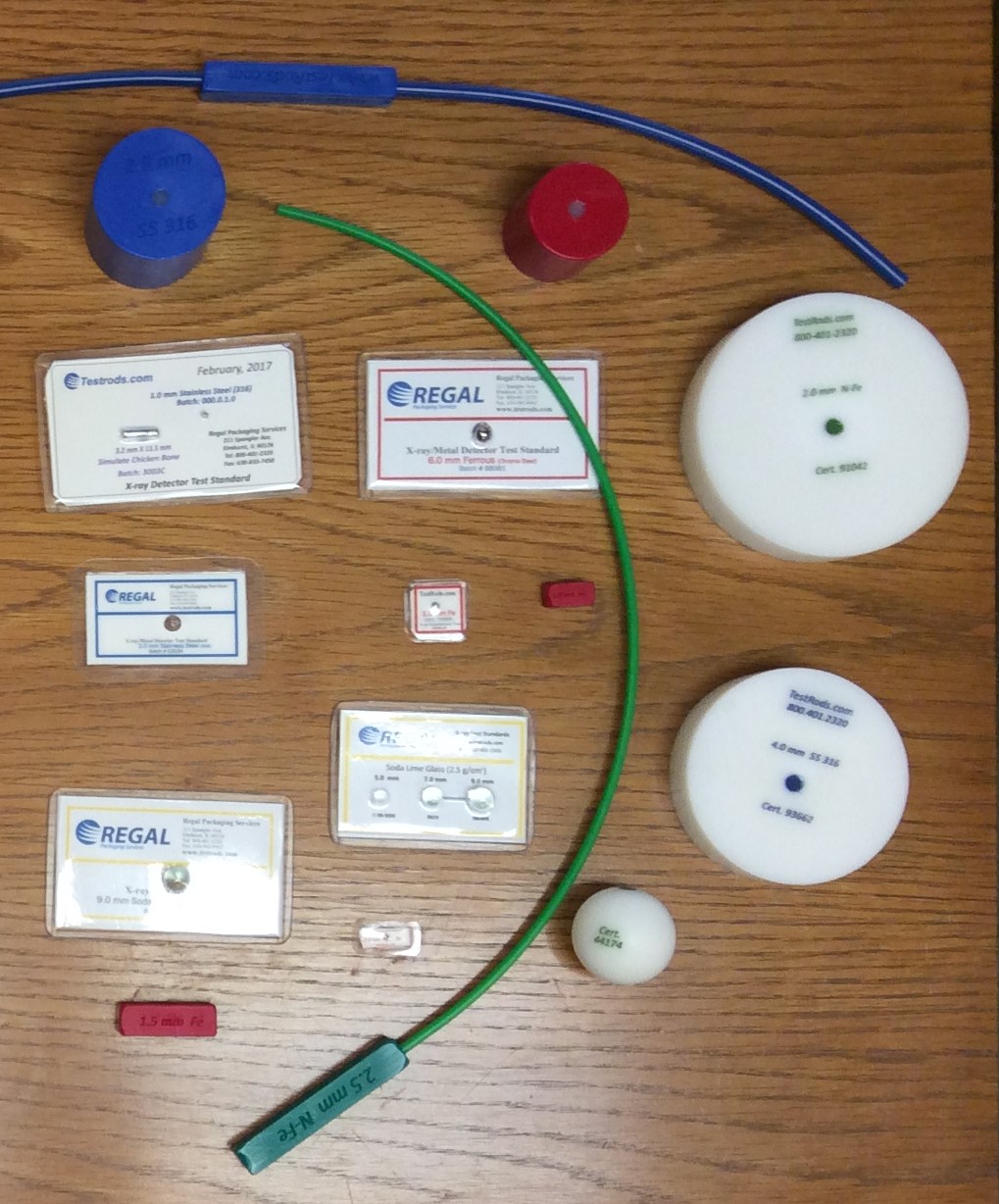
Custom Test Pieces
October 19, 2020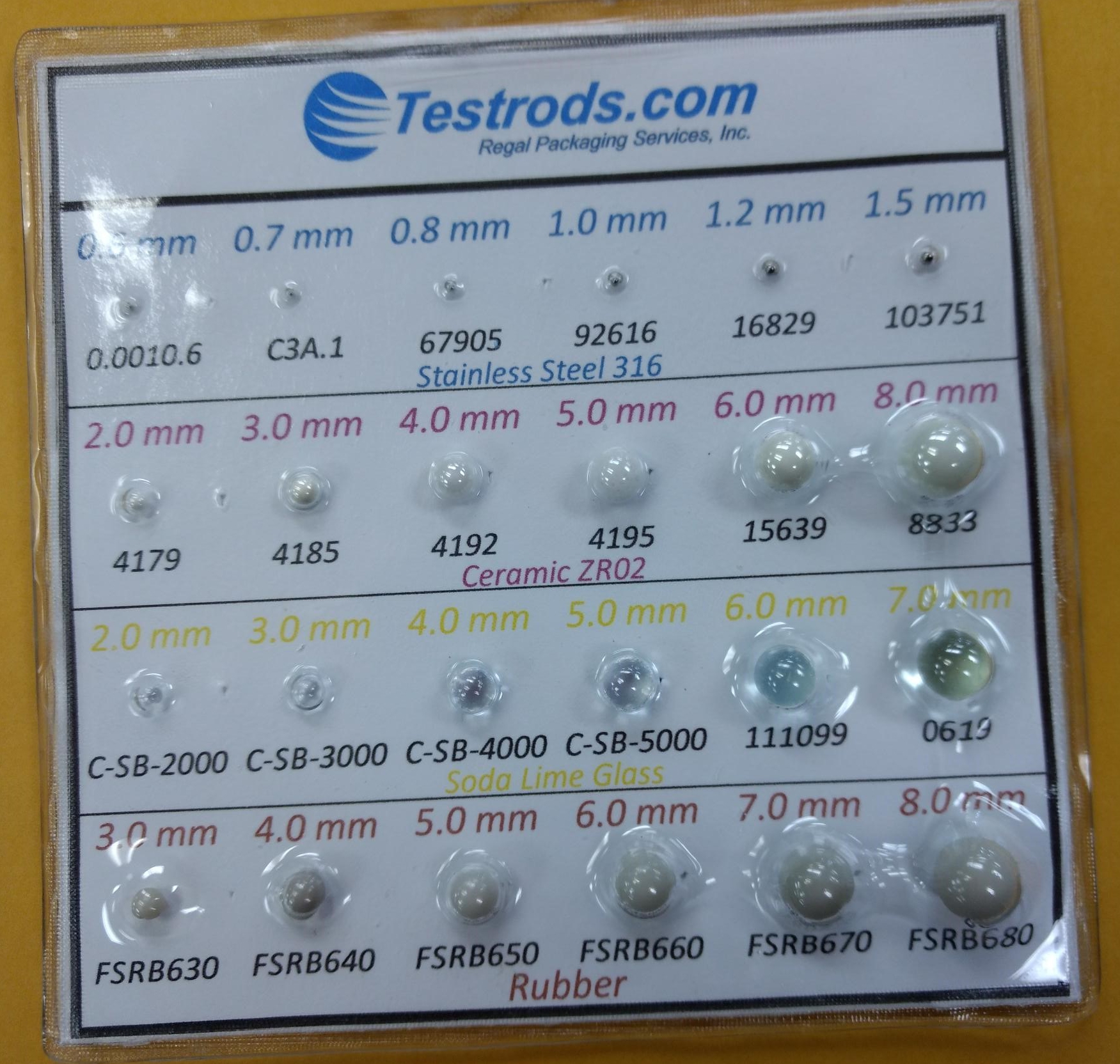
What are Thermoform Multi-Cards and Why Do I Need One?
February 4, 2021Types and Sizes of Metals
The sensitivity of a metal detector is dependent not only on the size of the aperture and the type of product you’re running, but also on the types and sizes of metals. For simplicity, all metals can be categorized into three types:
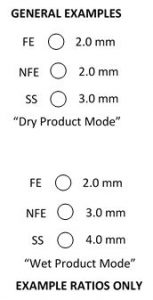
General Examples
Ferrous:
- Can easily be attracted to a magnet (steel, iron, etc.).
- Typically, the easiest metal to detect and usually the most common contaminant.
Non-Ferrous:
- Highly conductive non-magnetic metals (copper, aluminum, brass, etc.)
- When inspecting dry products these metals produce almost the same signal size as ferrous because they are good conductors.
- When inspecting wet products, decrease the sphere size by around 50%.
u>Non-Magnetic Stainless Steel:
- High quality 300 series stainless steels such as type 304, 316. 316 is the industry standard and should be used unless otherwise mandatory for some special circumstance.
- These are the most difficult metals to detect because of their poor
- electrical conductive qualities, and by definition they have low magnetic permeability.
- When inspecting dry products, a stainless sphere will have to be 50% larger than a ferrous sphere to produce the same signal.
- When inspecting wet products, the stainless sphere will need to be 200 to 300 % larger than a ferrous sphere to produce the same signal.
Orientation and Shape of the Metal
When it comes to types and sizes of metals, test pieces utilize spheres because they are the same shape from any angle. A true contaminant is rarely spherical and will produce a signal dependent on its orientation as it is conveyed through the aperture. The most dramatic example is shown by wire contaminants.
With wire, the signal produced will vary greatly based on the type of metal and its orientation as it passes through the metal detector (see image below). In a worst-case scenario, a wire may produce a signal no bigger than a sphere the same size as the diameter of the wire.
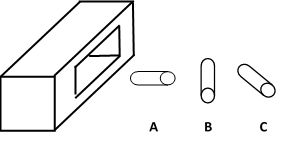
Shows the possibility of metal orientation
Ferrous Wires:
A – Easiest position, biggest signal.
B, C – Hardest Position, smallest signal.
Non-Ferrous and Stainless Steel Wires:
B, C – Easiest position, biggest signal.
A – Hardest position, smallest signal. Flow
In a sense, metal detectors are surface area detectors. They are calculating the types and sizes of metals. This has a considerable impact on determining the size of the metal you’re working to detect and set as your standard. For instance, you might think a 1.0mm Ferrous sphere is half the size of a 2.0mm Ferrous sphere. But a 1.0mm sphere has a surface area of 3.14mm2 while the surface area of the 2.0mm sphere is 12.57mm2. So the 2.0mm sphere will be (in a head to head comparison, not taking into account any product effect or other variables) 4 times easier to detect.
This is another reason that test standards are typically larger for harder metals to detect – like the Stainless Steel. More surface area means it’s easier to detect. More magnetic means it’s easier to detect. HACCP plans and standards are designed and evaluated with these difficulties in mind. An auditor should know that if a company is using the same size for all 3 metals, it’s probable they can be detecting smaller sizes of the ferrous and non-ferrous metals and may want to inquire why the smaller sizes are not being used.
A good Quality Control department will know about these difficulties in regard to types and sizes of metals as they evaluate, test and determine the HACCP plan for each product produced and then purchase the appropriate test pieces for ongoing testing.
2 Comments
I understand that surface area is a key influencer in detecting metal but would the same surface area but with larger volume (thicker) not alter the magnetic field more?
Todd that’s a really good question.
If I understand it correctly, you might have a scenario where a cube and a sphere have the same surface area, but different volumes.
The answer is that the surface area will conduct (interrupt or influence) the magnetic field generated by the detector more than its thickness.
For testing purposes, the reason we use a sphere is because it is not subject to orientation.
It will always represent a contaminant with the same surface area regardless of how it travels through the detector.
I hope that helps.