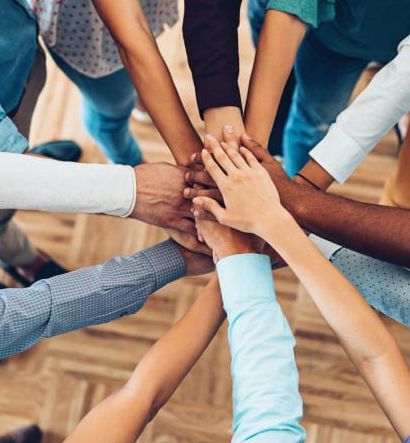
A Culture of Food Safety with the Right People
June 24, 2021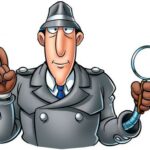
X-Ray Basics
August 24, 2021Metal Detection or X-ray Inspection
Metal detection (or X-ray inspection) acts as your first defense to identify foreign contaminants in food before they leave the manufacturing facility. Your selection of a system for detection involves quality assurance professionals, process engineers, and corporate safety executives. Together, you make the decision as to which kind of technology will protect a product from foreign contaminants. Most often, three criteria will the best detection point (hopefully near the center of the aperture), the application capability, and the cost-to-benefit ratio. Still, while these technologies have been used in food manufacturing for decades, hardware and software enhancements continue to develop new standards for quality. At times, this can create confusion about which method will work best for your application.
TYPE AND SIZE
The type and size of contaminant you need to detect (and the speed of the production line) can present a daunting challenge for any system. The challenge in front of you isn’t always finding the contaminant but in ignoring the product effect, the actual packaging, and/or the environment (vibration, radio transmission, etc.). You may have to deal with false positives, and that can add up to lost revenue, so the process requires dependability and consistency. In addition, detection systems in the food industry must be sensitive, operator friendly, as fully automated as possible, and cost effective. Moreover, the system must tolerate whatever conditions surround it, including a hot, moist, dusty, or even freezing environment.
PERFORMANCE
Three things govern performance: contaminant type detectability, smallest contaminant size, and likelihood or probability of detection. At the bottom of this article is a summary of contaminant types by technology as well as a table of densities for a variety of materials. These are only a general guideline. It is possible to miss contaminants or unexpected foreign objects you thought didn’t exist. This is especially true considering that metal detectors will not find anything but metals, and x-ray systems will rarely detect smaller size plastics or other contaminant types. As a general rule, x-ray systems will not find contaminants that float in water (like wood).
With X-Ray, you may find it works best to test many samples with different contaminants. At Testrods.com we designed a thermoform multi-card specifically for this purpose. You can choose from 10 different contaminant types including: Ferrous, Non-Ferrous (Brass), Stainless Steel 316, Aluminum, Soda-Lime Glass, Ceramic ZR02 and AL203, PTFE (Teflon), Acetal (Delrin), and Rubber in a wide variety of sizes. We can place as many different types and sizes on a single card as you need. That way, you can look at a single image and determine what types and sizes you can achieve. Once you know the capabilities of your system, you can purchase single contaminant cards for regular testing during production.
As an additional note, we have even developed a bone simulate card using precision cut aluminum. Using a multi-card for bone simulate, you can easily compare the bone you’re looking for against the various sizes of aluminum. Then, you can purchase single contaminant cards for regular testing during production. Call 866-977-8663 or email brian@regalpack.com for more information about multi-cards.
DETECTION
We define the probability of detection as the chance of missing a contaminant while producing real products at normal speed. Of course, the bigger the contaminant, the better the chance of detection. A Hazard Analysis and Critical Control Point (HACCP) plan should design and document management of the food safety process. Hazard Analysis determines which contaminant issues will occur. The Critical Control Point can appear in multiple places, so you need to examine the entire line for potential danger. Limiting or eliminating problems early in the process diminishes the cost of a product rework. You should never need to scrap an end-product to make the marketplace safe.
Ultimately, all these things will determine the best technology for your product. But it will also include: the type and size of contaminant, the speed of production, the type of product, the container/packaging, and the demands of the various CCPs. Make sure to educate and train your employees to think critically about all these variables, and then build a culture of food safety. Finally, make sure you have the best testing equipment at hand. Call us at 866-691-8560 or email testrods@testrod.com and let us answer any questions you might have. As a general guideline for metal detection or x-ray inspection, use the following breakdown.
Contaminant Type Met Det X-Ray
- Metal – Ferrous X X
- Metal Non-Ferrous X X
- Stainless Steel X X
- Aluminum X X
- Wire X* X*
- Ceramic X
- Glass X
- Rock X**
- Bone X***
- Plastic X
- Wood, pits, shells, insects, etc. ****
* Dependent on orientation
** Dependent on type and size
*** Only calcified bone and still very difficult based on animal type, age, etc.
**** Not conductive for MD or typically not dense enough for X-Ray
DENSITIES
- Polyethylene 0.857 g/cm3
- Polyvinyl 0.892 g/cm3
- UHMW 0.931 g/cm3
- Water 1.0 g/cm3
- Rubber 1.2 g/cm3
- PETG 1.38 g/cm³
- Acetal (Delrin) 1.4 g/cm3
- PTFE 2.2 g/cm3
- Borosilicate 2.23 g/cm3
- Soda-Lime Glass 2.5 g/cm3
- Aluminum 2.7 g/cm3
- Ceramic (AL203) 3.7 g/cm3
- Ceramic (ZRO2) 5.6 g/cm3
- Stainless Steel 316 7.82 g/cm3
- Ferrous 7.85 g/cm3
- Non-Ferrous 8.48 g/cm3
2 Comments
It’s interesting to know what type of contaminants an X-ray and a metal detector can identify. My dad’s been on the edge of a lawsuit ever since a client got injured eating their food products. I think my dad should implement strict detection solutions this month, so I’ll email your insight to him now.
Glad to be of service. I hope your dad benefits and also that his dispute with the customer is able to be resolved.