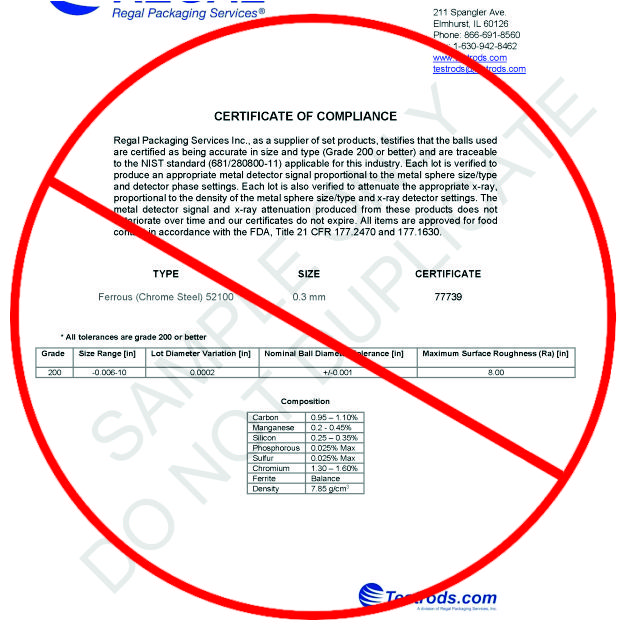
Is There an Expiration Date for Certificates of Compliance?
August 1, 2024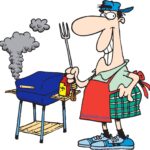
Stay Food Safe While Celebrating with Family and Friends
October 1, 2024
Aluminum vs. Brass in Metal Detection
Here at Regal Packaging Services, we are sometimes asked about using certified aluminum spheres for our test pieces. Brass has long been the standard non-ferrous material for testing metal detectors in the food industry. Brass is typically used because it has a high electrical conductivity property that metal detectors can detect. Brass is an alloy (copper and zinc) that is non-magnetic. All non-ferrous metals are detected by a metal detector through conductivity. Non-Ferrous metals create an electromagnetic field, that disrupts the detector’s magnetic field.
Interestingly, aluminum is exceedingly rare in native form, and the process to refine it from ores is complex, so for most of human history it was unknown. In fact, “Now ubiquitous and vital to modern life, aluminum was once more expensive than gold…The most familiar story of the first extraction of aluminum is that the youthful Ohioan Charles Martin Hall developed aluminum’s electrolytic extraction process in his family’s woodshed in 1886…The company Hall helped found drove the price down to below $1 per pound by 1891, and when a lightweight aluminum crankcase for their engine enabled the Wright Brothers to take their famous first flight, the metal was about $0.30 per pound.”1
“High purity aluminium is a soft material … which limits its usability in industrial applications.”2 This may be another reason brass was chosen as the standard for metal detection testing in the food industry.
However, because some companies have aluminum components along the production line, there’s always a concern that testing should be required for that type of metal either in place of, or in addition to, the brass.
FDA regulations3 state that a company must:
“Develop sensitivity standards that are based on whether the potential hazard is ferrous, non-ferrous, or stainless steel, or obtain such standards from the equipment manufacturer.” Unfortunately, it does not specify what type of ferrous, non-ferrous or grade of stainless steel should be used in testing. When it comes to ferrous, there isn’t really a better choice than chrome steel. “Chrome plating steel is any type of steel that has been mixed with chromium with the aim of preventing rusting. This type of steel has undergone a process known as chrome plating.”4
Stainless Steel (alloy) 316 is the best choice for this kind of steel. 316 is the least magnetic or conductive of the stainless steel alloys used in the industry. The simple theory is that if you capture and reject SS 316, you’ll also be rejecting 304 and other types of stainless steel. Conversely, if you test using 304, you may not be rejecting 316.
So, what about non-ferrous? In our own in-house testing, we have found that aluminum and brass will perform (be detected) nearly identically in both wet and dry modes. What’s critical then, is choosing the metal which is most commonly found on your production line and writing that into your HACCP plan and SOPs. If any change is to be made, thorough testing should be done before implementing any new practices.
But there is one benefit to using brass over aluminum, and that is its availability within the test piece market. There is a much wider variety of sizes available in brass than you will find in aluminum. So, for instance, you might find 2.8mm Brass, but you may not find 2.8mm Aluminum. So if your standard isn’t a common size, getting the right aluminum test piece may be difficult.
There is also a vast difference between aluminum and brass in x-ray inspection. Aluminum is much less dense (2.7g/cm3) than brass (8.48g/cm3). So comparably, while brass would be easily visible, aluminum would be harder to detect. And if the goal is to keep as many contaminants as possible out of the product, then using a lower density material for testing just makes good sense, so long as the product density itself doesn’t interfere with the test standard visibility.
The bottom line, in general then, is that it’s a good idea to maintain the industry standard use of brass over aluminum unless your HACCP plan and SOPs have been written specifically for aluminum and you have aluminum on your production line. You’ll find aluminum and non-ferrous (brass) testrods, acetal test cards, laminate cards and thermoform cards right here on our website.