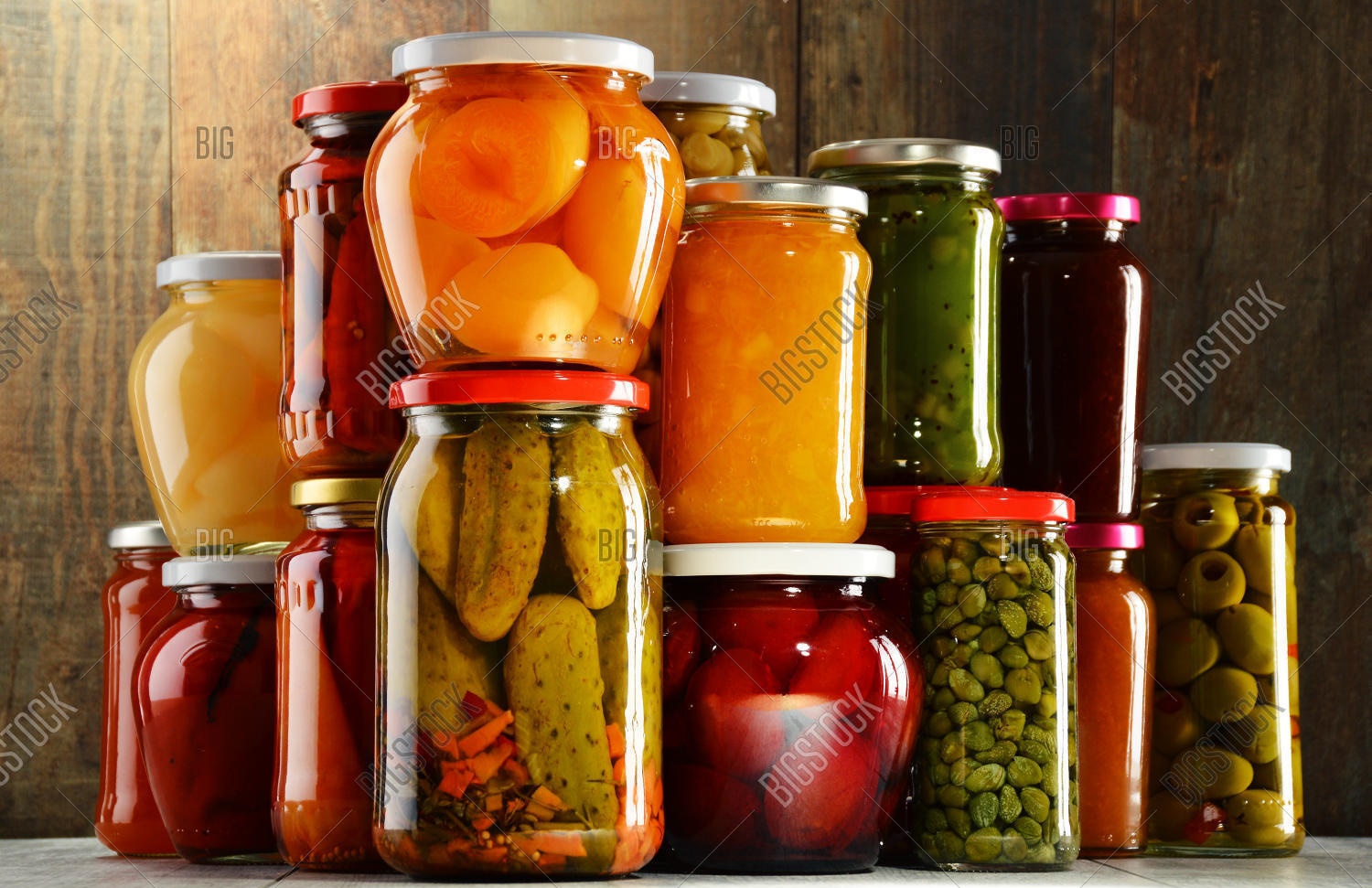
What’s New With The Food Safety Guidelines
June 3, 2019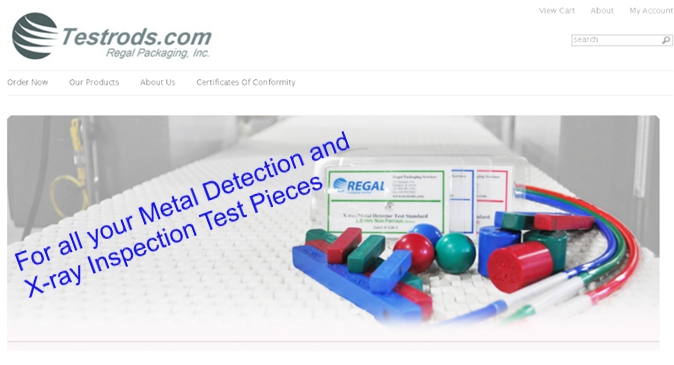
X-Ray Systems Test Pieces
June 12, 2019What to Look for in a Metal Detector Test
A metal detector test is a vital part of any food manufacturing and packaging process. Running frequent tests is a necessity with metal detectors. It is the only proven way to avoid the presence of contaminants in a company’s final product.
Even one case of contamination can open a company up to potential lawsuits, negative publicity and costly downtime for repairs. It makes sense for any company to do everything they can to avoid contamination. That means relying on metal detectors placed within the production process.
The type of detector used can vary depending on the product being scanned. Detectors can vary in shape and size. Still, all of them work on the same principle, using a three-coil system. Each is designed to detect the presence of ferrous, non-ferrous, or stainless steel metals in a product.
How It Works
As the product passes between the coils, any metal will create a disturbance in the high-frequency field created by the coils. When a disturbance is detected, the machine will automatically reject the product, preventing the contaminant from reaching the marketplace.
Though it seems like a simple method, a metal detector can actually be negatively affected by a number of variables. The size of the opening that the product passes through (the aperture) can affect a detector’s sensitivity. The larger the opening, the further apart the coils need to be placed, making them less sensitive. Similarly, the closer a product is positioned to the center, the less sensitive the detector is, as the coils are farthest apart at this point.
Other Factors
Another key factor in testing with metal detectors is the composition of the product itself. Certain properties, such as moisture content and mineral content, can affect the test results. The existence of salt, acid, fat and some vitamins may produce false positives. Also, external factors, such as vibration and electrical interference from other machinery, can affect the sensitivity of the metal detector. To counter these, you need to carefully calibrate your detector to the product and the environment to ensure optimal results. Once that’s done, standard metal sizes for testing can be determined. These standards should be audited by a third party company. Regal Packaging Services (see detectoraudits.com), can provide that service and demonstrate compliance to the HACCP plan.
Aside from sensitivity, the positioning of the detector itself within the production process can be extremely important. Having a detector at the beginning of the process can help to eliminate any contaminants in the base product. Testing at the end of the process can be a good fail safe to ensure the safety of the final product.
Failure
It is also possible (or maybe even probable) for machinery used throughout the process to break down. Contaminant could then spoil the product at any point. So the ideal procedure is to put a metal detector at several points along the production line. If contaminant is detected along the way, it will be easier to isolate and repair the source of the issue.
Equally important is ensuring that the detectors themselves are operating properly. This can be achieved by running regular tests using specially designed test pieces such as those manufactured by Regal Packaging Services.
With decades of experience, Regal understands the unique aspects of metal detection. It is why we work with each customer to meet their individual needs. And we use only the highest quality metals, certified to NIST standards, in our test pieces. We provide a range of shapes, including spheres, rods and cards, to fit any kind of detector. And each piece is individually certified and designed to withstand the rigors of regular testing. We consider the base product, which is FDA approved, to be nearly indestructible.
By running one of our test pieces through your system on a regular basis, you’ll be able to quickly identify any problems with your detectors. The importance of this kind of metal detector test cannot be stressed enough. It’s the only proven way to ensure that your products are clean and safe, which means keeping your customers happy.
You need to know that every time you run a metal detector test you’ll get results that you can count on. With quality test pieces from Regal Packaging you’ll know you’re in good hands because we make it our business to keep your business up and running smoothly.