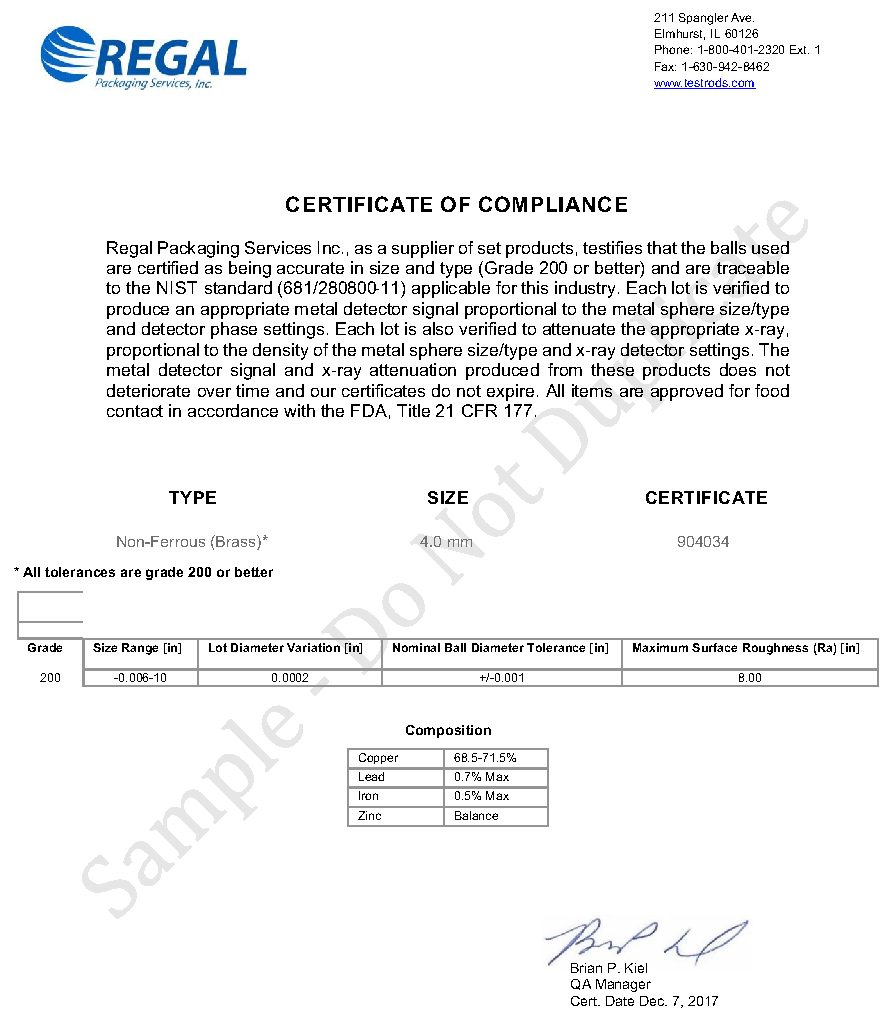
Why Do I Need Certificates of Conformity
January 9, 2019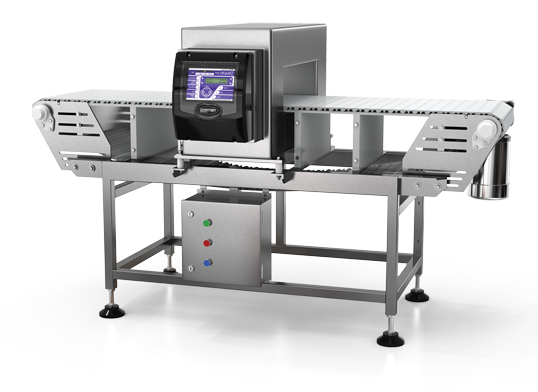
Metal Detector Setup
March 28, 2019Commitment to Food Safety
After working in the food industry for a while, I’m impressed by the professionalism and commitment to food safety I see. Or at least what I’ve seen from the companies who have utilized what Regal Packaging Services has to offer. And I don’t mean that as a pat on the back. I say that because we’re intimately familiar with the industry. And while not every company we do business with is an expert, there is a genuine concern for the marketplace. And clearly, there is an effort to put safe products in the hands of the customer. That’s not only true because of the legal or economic concerns, but also because of the ethical and moral considerations.
A 2015 article of Time noted that, “It’s … not so surprising that metal pieces end up in food products.” And, “given our industrialized food system. … When it happens in the food chain, that’s downright dangerous.” But companies who care, while regulated and guided by the FSMA, etc., develop HAACP plans to mitigate the dangers.
Our Experience
Regal Packaging Services has been in business since 1998, selling, servicing Fortress Metal Detectors. And we also audit all brands of metal detectors (and x-ray systems). So we have to know as much as humanly possible about the metal detection process as a whole. We also sell our own line of test pieces with the capacity to custom manufacture nearly every imaginable test piece. We are genuinely committed to food safety.
We continue to grow and have seen success at all levels. That’s true in part because of a shared concern for keeping metal and other foreign matter off the dining table. And it’s not just a concern, it’s a positive persistence at safety. We help companies meet the challenges of the industry and their own HACCP plans. And we do that by providing them with the hardware, but also the knowledge required to preempt metal detection issues.
How We Help
It’s not unusual for us to get a call from a company that’s just beginning the metal detection process. They may also be developing their procedures or HACCP plan. Some are unsure what standards they should be achieving for their product. Is it 1.0mm Ferrous, 1.5mm Non-Ferrous and 2.0mm Stainless Steel 316? Because our salesman and technicians have decades of experience, we have the ability to ask the right questions. We can help our customers determine what success should look like for their application. A given product in a specified aperture can generally be expected to meet certain standards (with consideration for other factors). We then help them get a close read, or starting point, for their specific need. Customers may not know what type of test pieces they should use. Or they may have a manufacturing or packaging process that requires a custom solution.
We’ve met every challenge for custom metal detection and x-ray inspection test pieces, including a variety of shapes and dimensions.
ISO Certified
The Testrods division is ISO 9001:2015 certified because we believe that our processes need to be clear and documented. It means we’re held accountable for they way things work both in manufacturing, sales and customer service. We test and retest products. When we send an order out, we know it meets the standards necessary for our customers’ success in food safety. And we source our materials from the right sources so we know they can be trusted.
Before a company puts food on a customer’s table, it should create a climate of quality in its business and in the minds and hearts of its employees. William A. Foster once said, “Quality is never an accident; it is always the result of high intention, sincere effort, intelligent direction and skillful execution; it represents the wise choice of many alternatives.” At Regal Packaging Services, everything we do is about food safety.